Un succès commercial
Le X-4°, second bateau de la gamme Pur X renoue avec la notion de croiseur confortable, qui peut de temps à autre s'aligner sur le départ de régate avec un potentiel de victoire. Elle connait un vrai succès depuis son lancement. Plus d'une centaine d'exemplaires ont été fabriqués depuis deux ans. Cinq modèles, du 40 au 65 pieds sont au catalogue 2019 et on attend l'annonce d'un 56 et sans doute d'un 60 pendant l'hiver.
Des lignes modernes
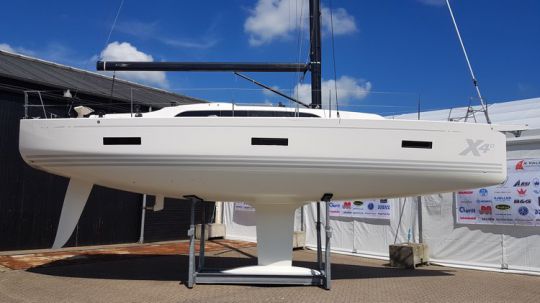
Comme pour tous les modèles, la conception provient du Bureau d'étude dirigé par l'un des trois fondateurs de la marque, Niels Jeppesen. Les choix architecturaux sont assez conservateurs, mais exécutés avec un certain modernisme. La ligne générale avec les hublots de roof est plus proche des Xp que des Xc.
Un petit 40 pieds
Un bouchain légèrement marqué se dessine au deux tiers de la longueur et se relève vers la poupe. Son étrave droite avec un bout-dehors en option participe à le baptiser 4°, car la longueur de coque n'est que de 11,50 m (et non 13 m d'un 40 pieds). L'unique safran, dessiné en forme de demi-queue de baleine, est commandé par deux barres à roue.
Un châssis acier pour la rigidité
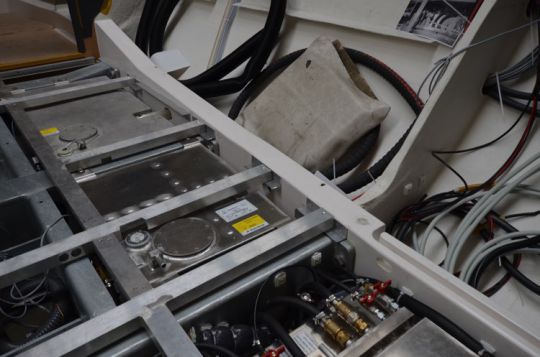
La liaison coque-pont est à l'intérieur du livet plat qui fait partie intégrante des flancs. Ce procédé est rendu possible par l'utilisation de deux demi-moules pour infuser la coque. La quille en T est munie d'un bulbe torpille, comme la gamme performance. Son voile est fixé à la coque par boulonnage sur le fameux châssis en acier galvanisé qui joue le rôle de varangue et reprend les efforts du gréement. Il sert aussi pour élinguer le bateau depuis un point central, preuve de la maitrise de l'équilibre par les concepteurs. Par contre, au lieu d'être stratifié à la coque, il est maintenant boulonné sur deux épais longerons en fibre de verre intégrés à la coque, encore plus fiable, pratique et plus résistant en cas de talonnage.
Une qualité qui se paye en temps de main d'œuvre
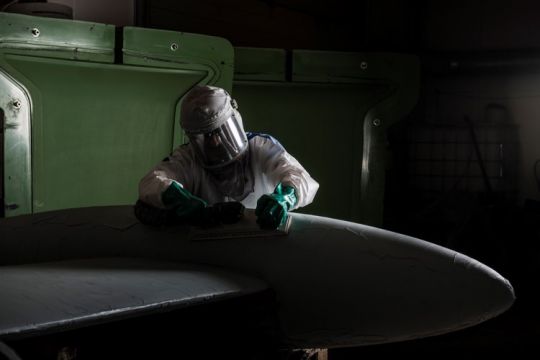
Coques et pont sont en sandwich résine époxy/verre/mousse cellulaire, infusés sous vide et cuit ensuite à 80° pendant 24 heures. Le compromis rigidité/résistance/poids est donc favorisé au maximum. Le remplissage manuel des champs de découpe, les renforts autour des hublots de coques, l'ajustement des cloisons dans les contre moule de pont et les couches de tissu mat sous le gelcoat, sont des marqueurs de la grande qualité de fabrication qui nécessite tout de même plus du double de temps passé sur chaine que des modèles de plus grandes séries.